Herrenstein
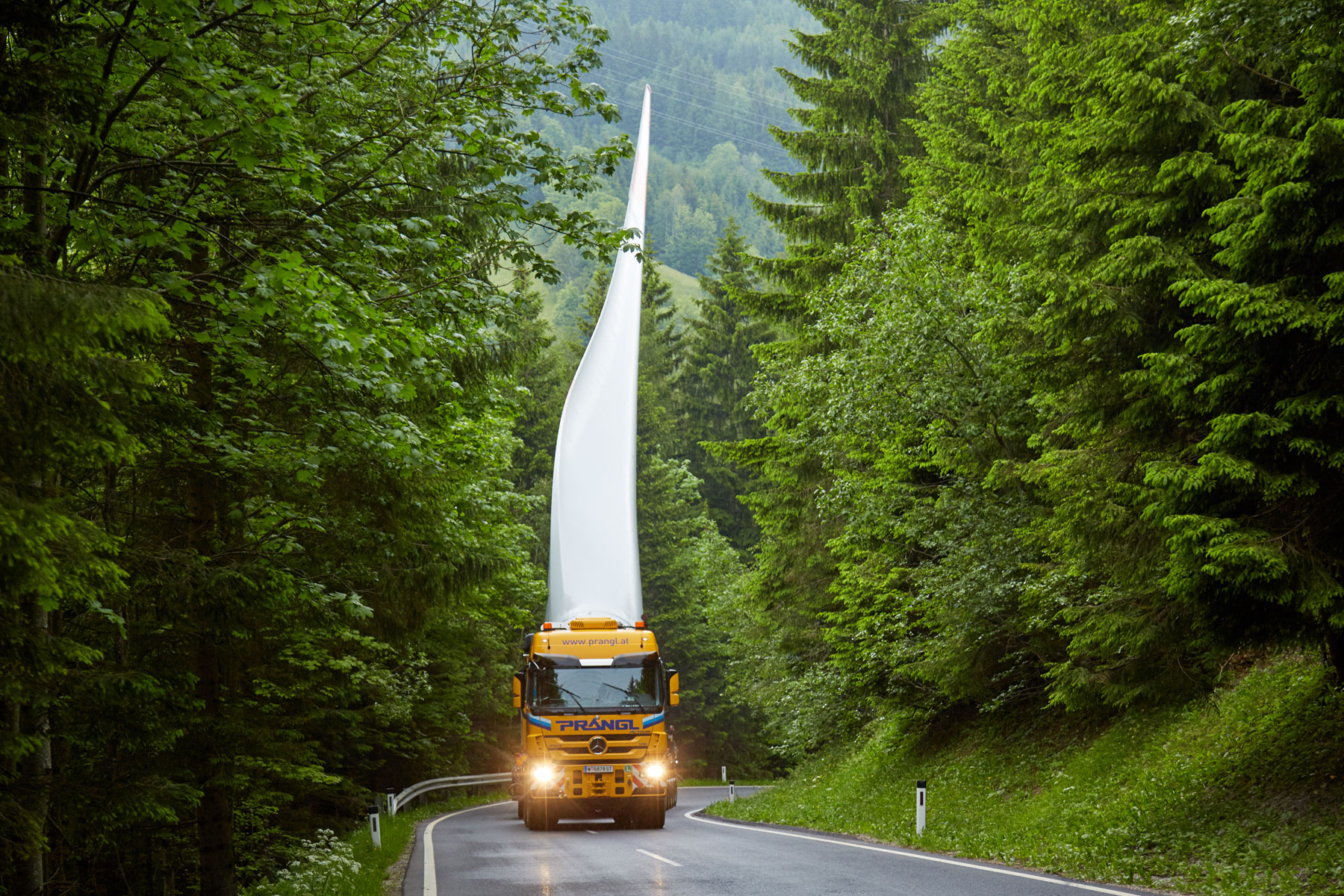
The challenge
Feasibility study for the Herrenstein wind farm
Prangl was commissioned to conduct a feasibility study for the Herrenstein wind farm back in October 2013. It was only this expertise that secured the feasibility and finalisation of the project in the first place. This was checked again two years later – for larger wind power plants. This study, which was again conducted by Prangl, also gave a positive result.
Our solution
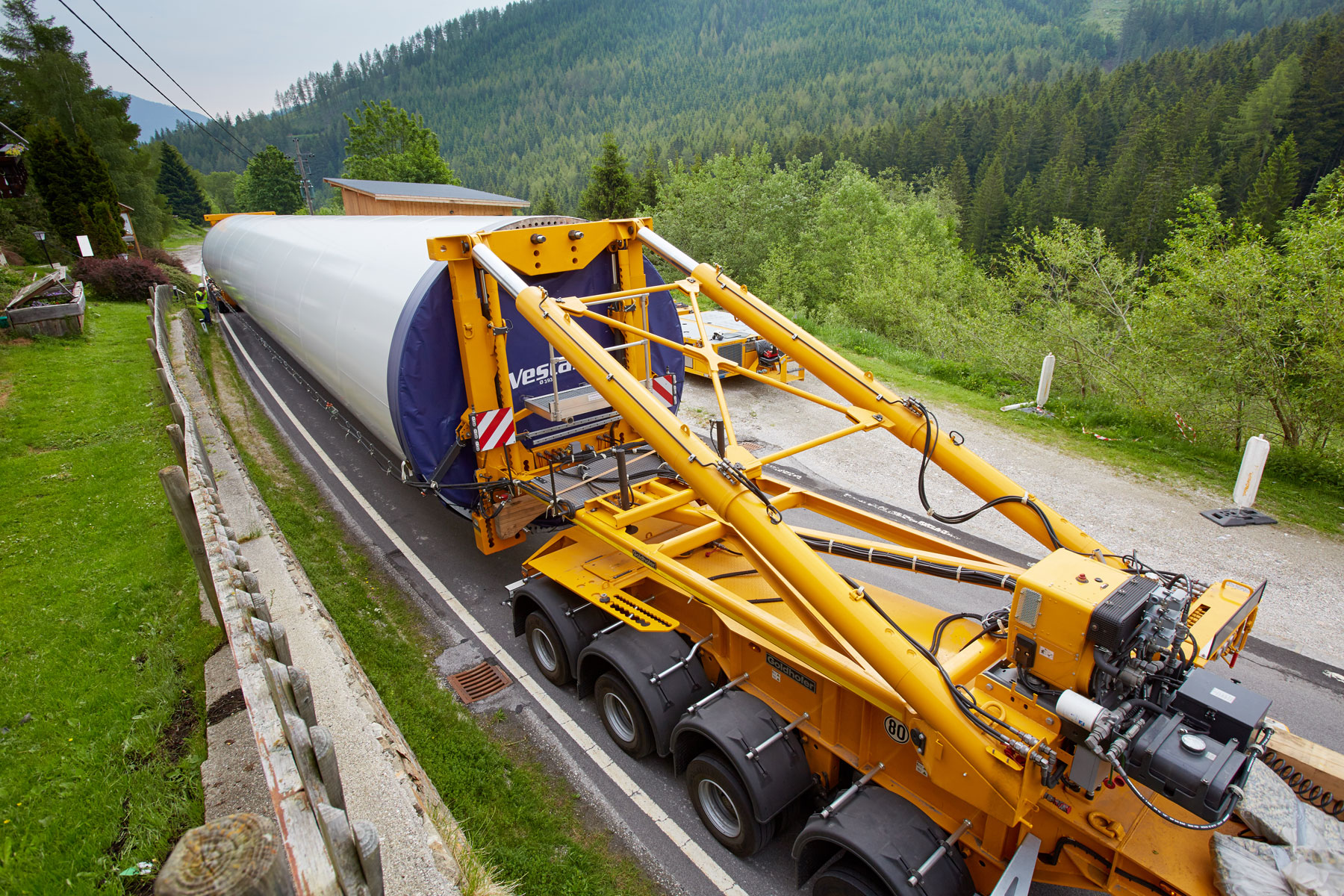
Austria's highest wind turbines in an Alpine location
The plants are located in the Hochwechsel region at an altitude of approx. 1,400 metres above sea level. The six wind turbines with a hub height of 94 metres and a rotor diameter of 112 metres are currently the largest wind power plants that have been erected in the Alpine region of Austria. Prangl was exclusively commissioned with all the logistics activities to ensure that the project ran smoothly: The delivery of all components, intermediate storage, mountain transport and the erection of cranes.
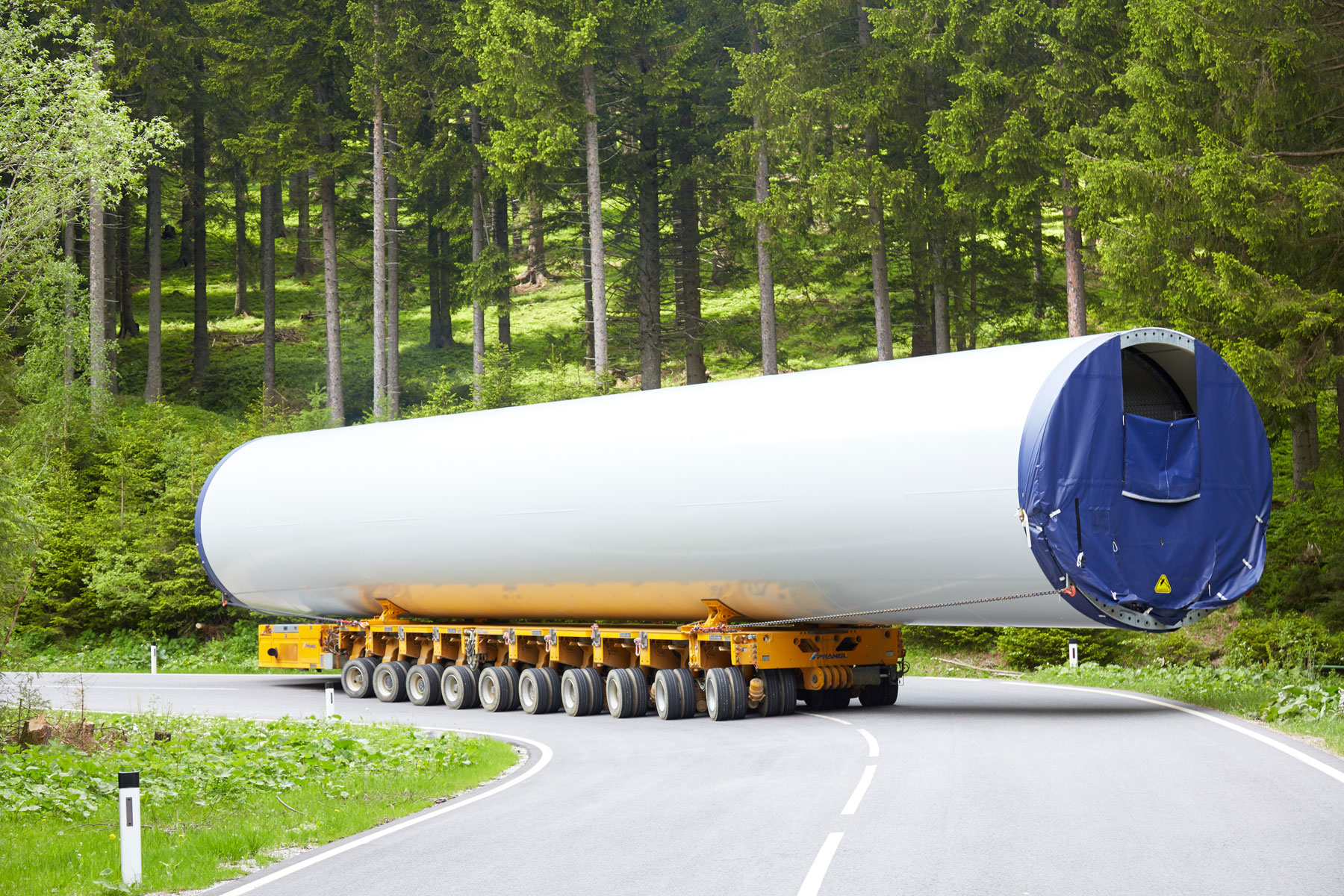
Spectacular transfer to the self-propelled heavy-duty trailers
The road transport of the 62 ton steel sections had an overall length of 55 metres. There were two bends on the Feistritzsattel mountain pass that were impassable with this overall length. The tower shots therefore had to be transferred to a self-propelled heavy-duty module. The load had to be transferred without a crane due to the lack of space. The technology chosen to transfer the load has never previously been available anywhere in the world. The self-propelled heavy-duty module was manoeuvred by remote control under the 1.7 metre high freely rotating tube adapter. The adapter vehicle was then lowered and the steel section was placed on the self-propelled trailer and actively taken over by it. Then it started the approximately 17 kilometre trip up the mountain.
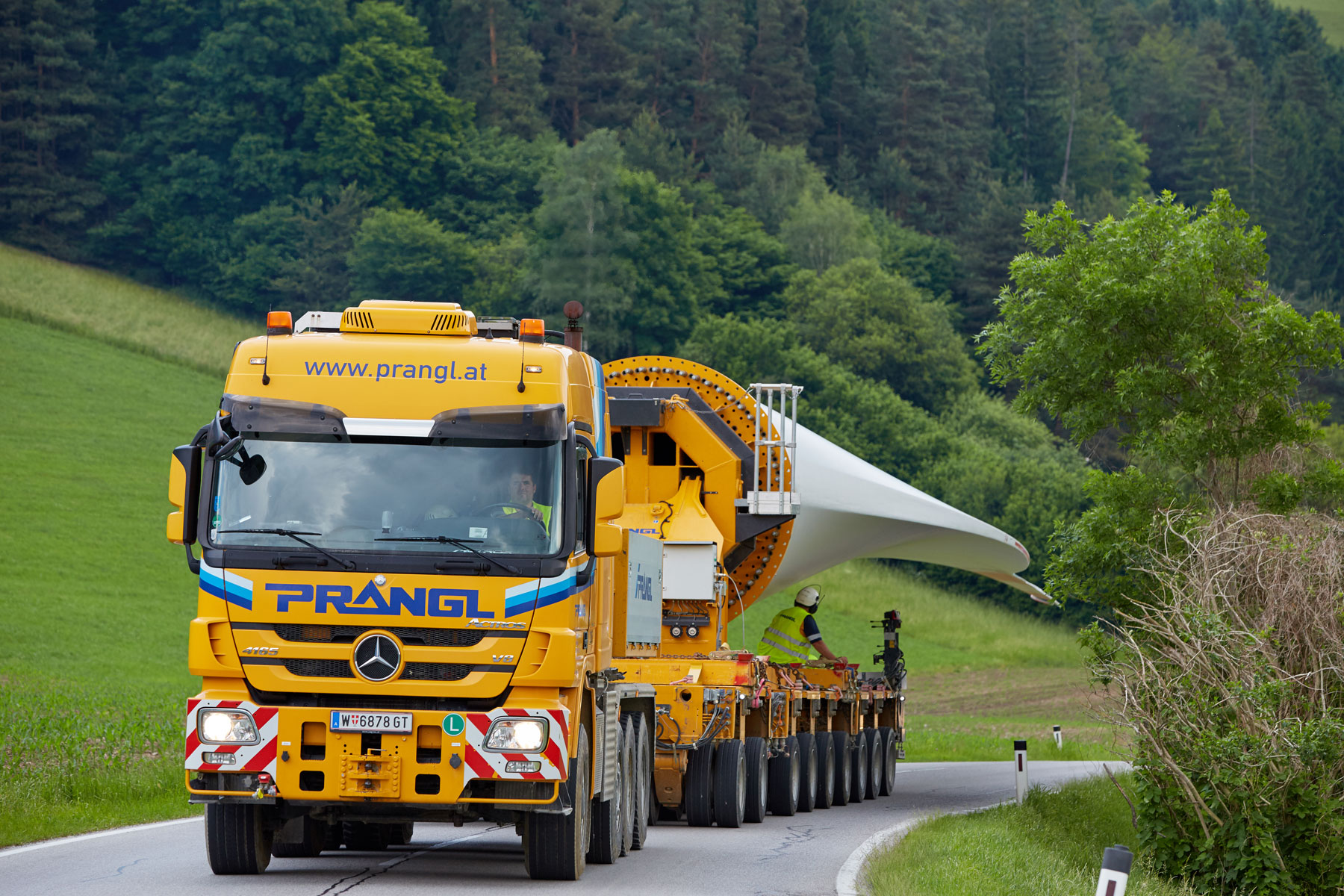
Blade transport device on module axle trailers with four-wheel drive tractor unit
It was also the first time that nearly 55 metre long rotor blades had been transported in Europe. While Prangl's blade transportation equipment had previously only ever been mounted on a remote-controlled self-propelled trailer, this time it was mounted on modular axle trailers in combination with a four-wheel drive tractor unit. Although the self-propelled heavy-duty modules are more manoeuvrable, they can only move at walking pace. This would have been too slow and inefficient and would have blocked the traffic in particular on a remaining stretch of 39 kilometres. Speeds of up to 30 km/h could still be achieved with road-approved axle modules – despite the enormous overall length of 73 metres.
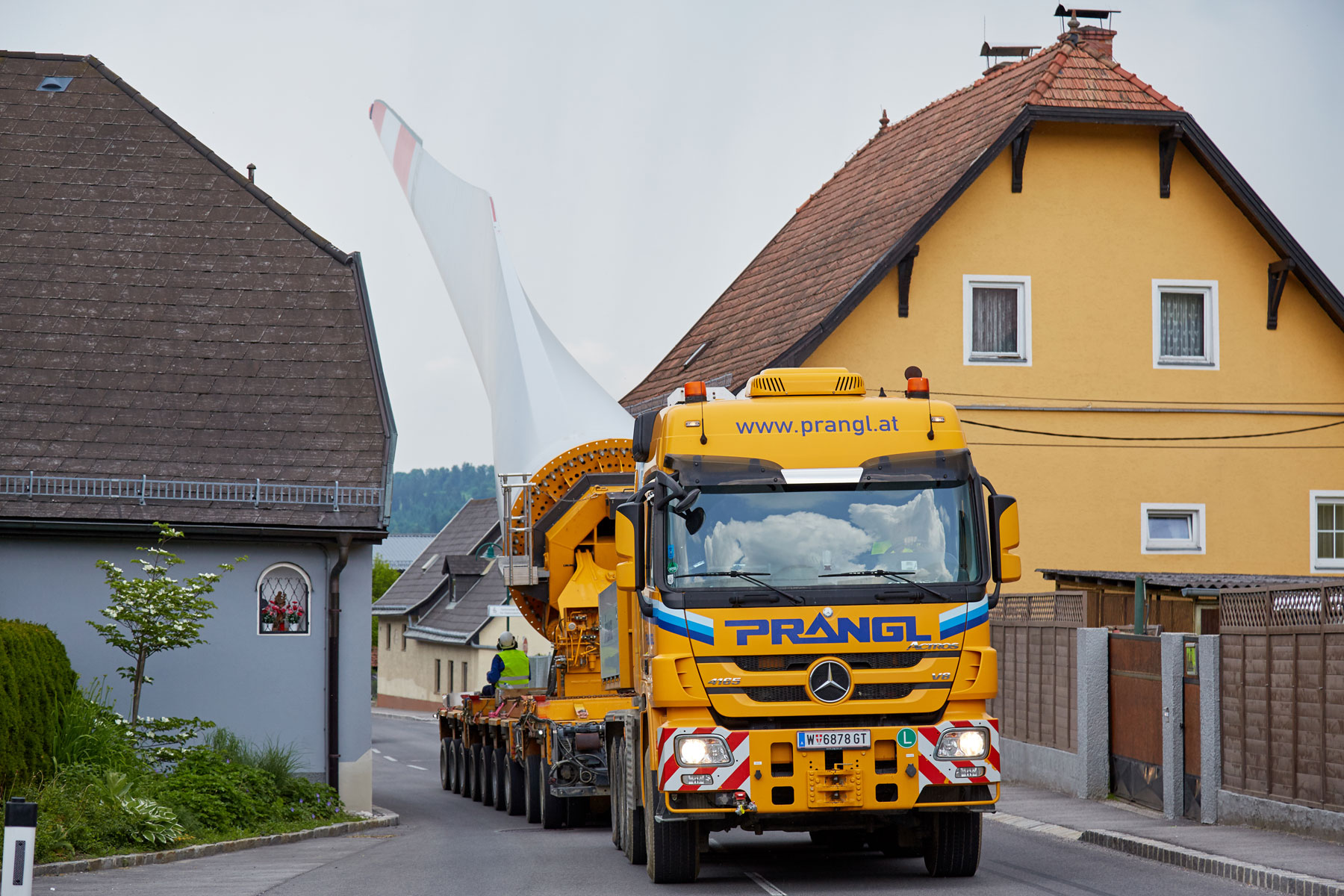
High flexibility as an unrivalled benefit
In total, 86 power and telephone lines had to be passed under so the rotor blade could not be constantly positioned at 60°. Only six of the above-mentioned lines had to be removed or relocated due to the high degree of flexibility and mobility of the transport combination selected. All other lines were able to be passed. This also facilitated the overall logistics enormously.
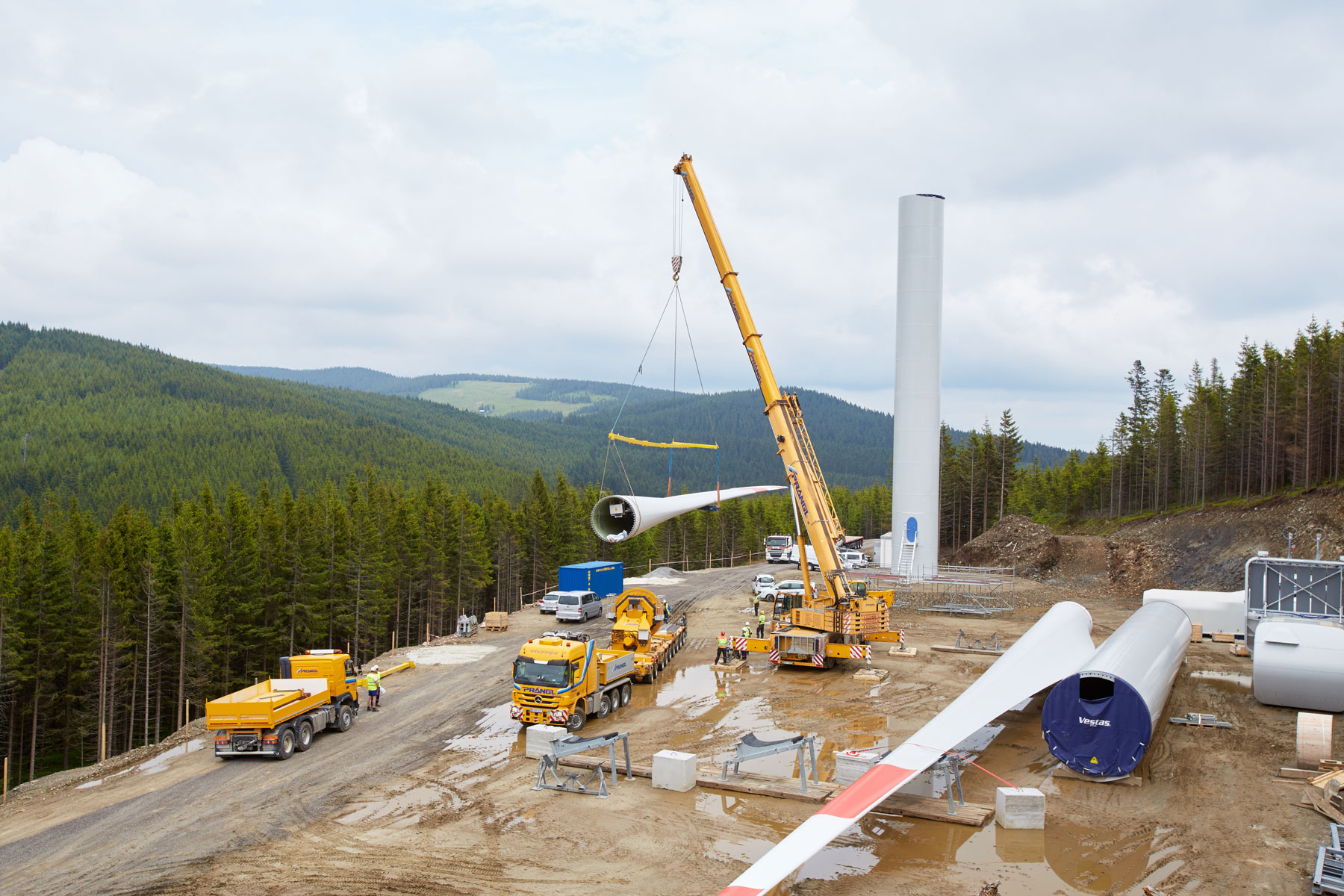
Additional pusher vehicle for the particularly heavy components
The main logistics site was set up at approx. 1,000 metres above sea level. The components then had to be moved approx. eight kilometres with gradients of up to 16% to their storage location. These journeys were made with 10-axle self-propelled trailers and four-wheel drive trucks with heavy-duty low-loaders. The existing transport combination was supplemented by an additional pusher vehicle for the heavy components to be able to cope with the steep approach into the wind farm. The upgrade of the access routes could therefore be reduced to a minimum.
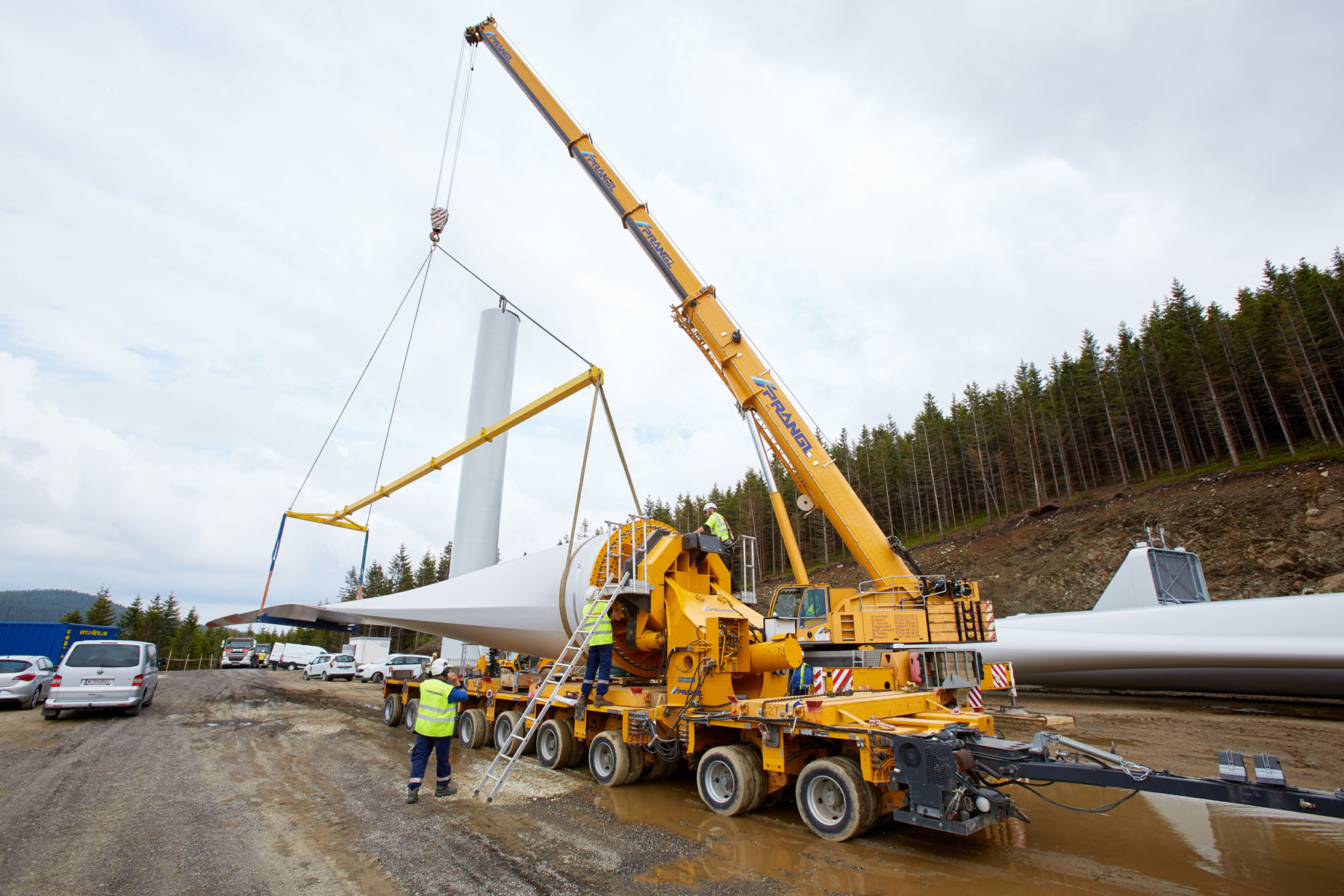
Assembly with a 500-tonne telescopic crane and a 600-tonne lattice boom crane
The wind power plants were pre-assembled with a 500 tonne telescopic crane and the main installation was undertaken with a 600 tonne lattice boom crane. The perfect cooperation between the multi-member team also resulted in the optimum realisation of such a highly complex project. The wind farm was able to be completed one week ahead of schedule thanks to the excellent planning and the perfect cooperation between all parties involved – and this was also achieved despite the fact that the project had to start two weeks late because of the late snowfall.
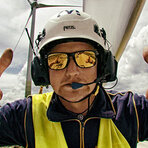