Combined heat and power plant
Richard Rieder
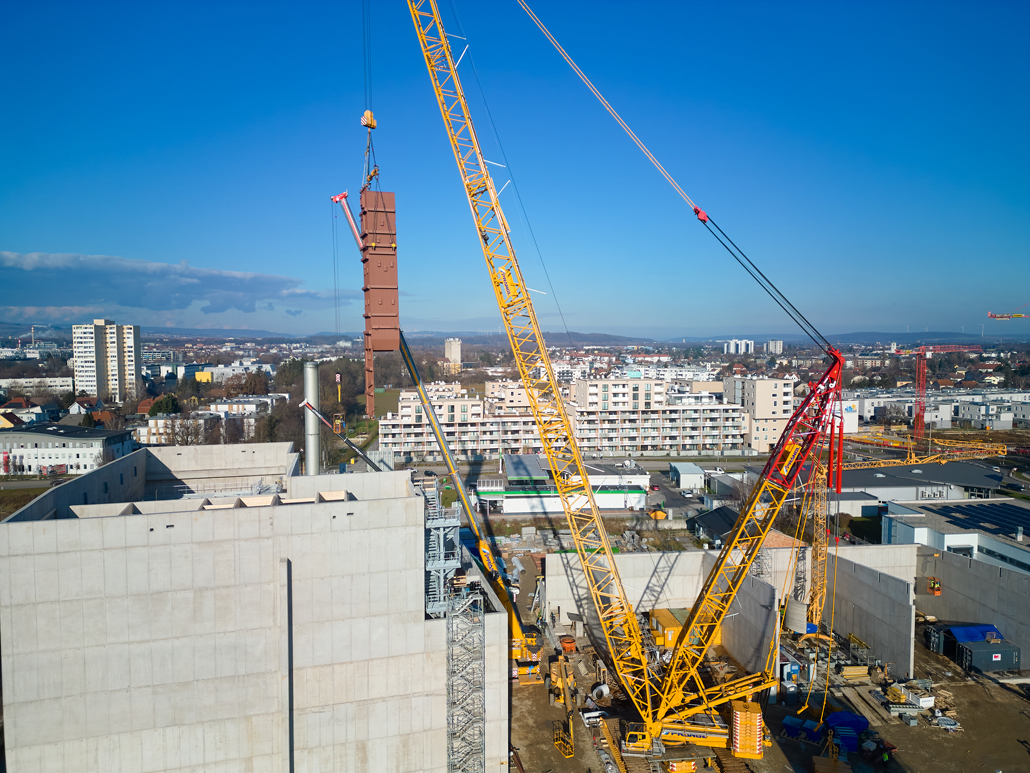
The challenge
Constructing a combined heat and power plant
In order to increase the proportion of environmentally friendly energy in the district heating network in St. Pölten, the city and EVN jointly decides to construct an ultra- modern biomass combined heat and power plant in the east of the city. Prangl was entrusted with the sensitive lifting work and racked its brains over a suitable concept that contained both the exact process scenarios and the optimum machine selection.
Our solution
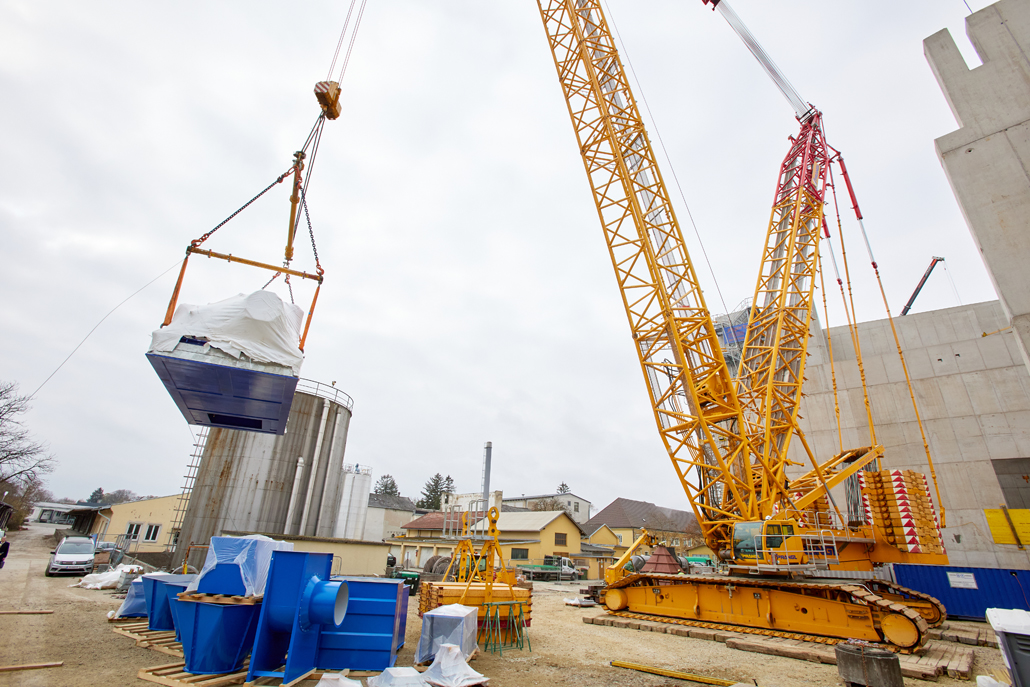
The optimum equipment is in demand
The combined heat and power plant that has been used for district heating in St. Pölten, which is around 30 years old and operated using natural gas will soon be worn out. The new bio combined heat and power plant will be “fed” with around 1000 loose cubic metres of wood chips per day and can supply the district heating with sustainable natural heat in the future. In order to move the individual parts of the combined heat and power plant efficiently and safely to the site location, the special requirements for the machines regarding lifting weight, projection, hook height and the somewhat limited space on-site had to be considered.
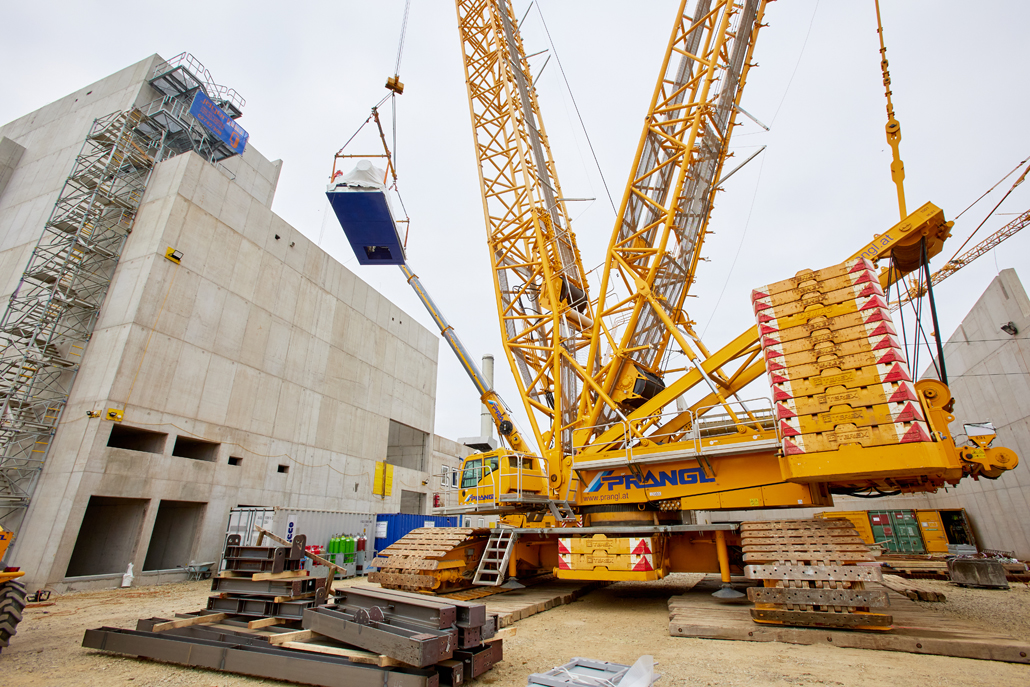
650-tonne crawler crane
The work started by unloading the HGVs that delivered the parts. An 88 metre-tonne mobile construction crane with crawler chassis handled the steel parts to prepare them for the large lifting processes. In addition, a 250-tonne telescopic crane, a telehandler, a telescopic boom lift and a special work platform were used to support the preparatory work. A 650-tonne crawler crane was also placed precisely on the building site for the heavy lifting. It was first used to lift “axle holding fixtures” weighing 22 tonnes each. A large audience was then present to view the 45-tonne steam turbine.
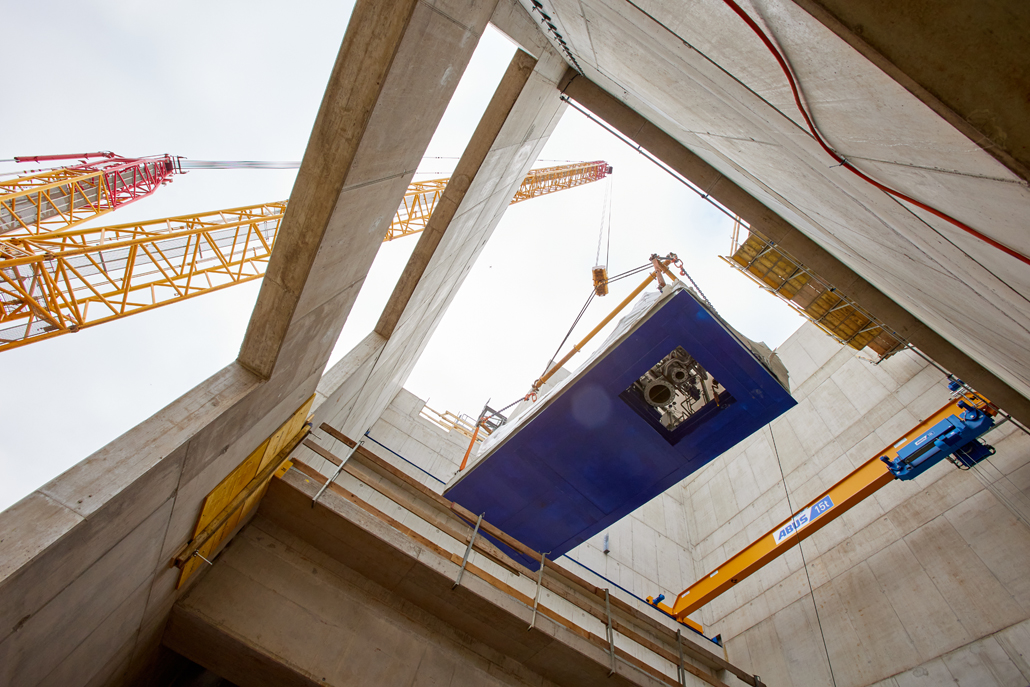
Tricky loads
In order to overcome a 28-metre projecting edge, the turbine was lifted using a crawler crane with a projection of 50 metres and a hook height of 60 metres. The heavy load was lowered carefully and to the centimetre into place between the walls in the turbine room. A total of eight Ekos each weighing 22 tonnes then followed. The heart of the new plant is the boiler that was next up. The boiler walls were moved in using several lifting processes. The heaviest wall weighed in at 55 tonnes. In total, the finished boiler weighs 70 tonnes and is 23 metres long, 4.5 metres wide and 3.5 metres high.
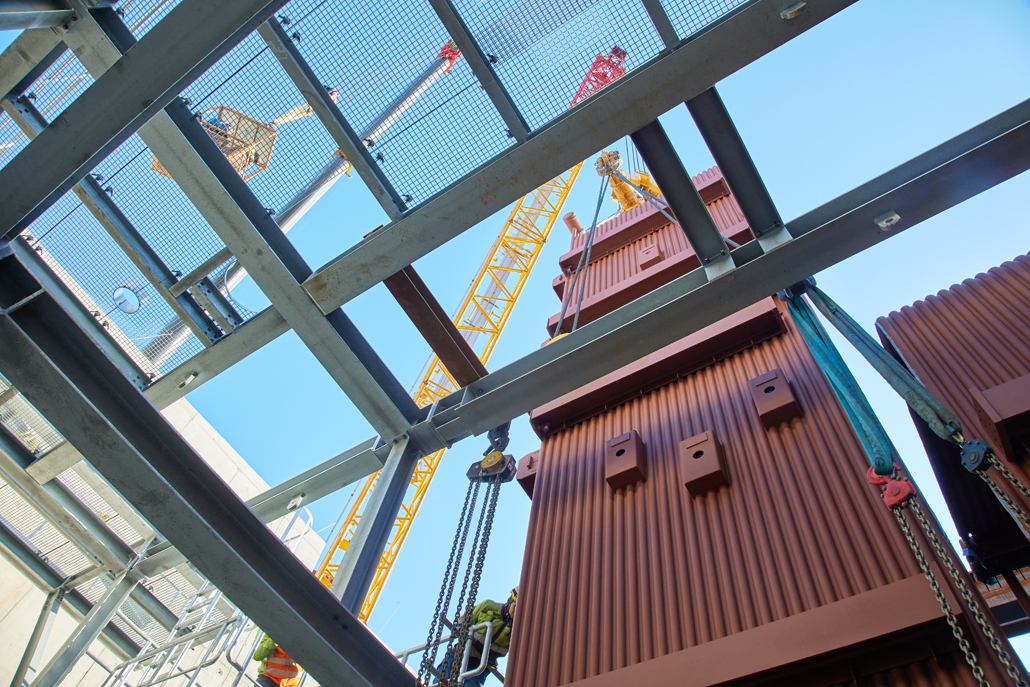
Maximum precision
The highest precision was required again for this job. In order to be able to place the parts in the exact right position, the experienced Prangl team took on the roles of marshallers. The parts to be lifted were also lashed by Prangl specialists, as this turned out not to be so easy die to the asymmetrical centre of gravity on the parts. Despite the challenging task, everything went perfectly. The new biomass combined heat and power plant will supply green energy to 15,000 and heat to up to 30,000 homes from January 2026. And it will save around 25,000 tonnes of CO2 per year.
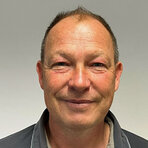